Ndfeb hydrogen decrepitation.jpeg.
Mar 1, 1985 · The hydrogen decrepitation (HD) process are studied in detail based on these results. The hydrogen absorption mechanism of Sm(CoFeCuZr) 7.6 alloy can be regarded as a hydrogen dissolution process without phase transformation. In addition, the existence of a large amount of fine grains in the SC has an adverse effect on the alignment, which can ...
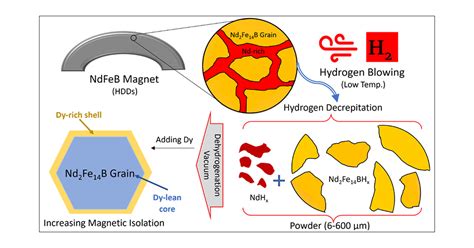
NdFeB ingot exposed to hydrogen atmosphere due to the changes of hydride lattice parameters cracks. The process called HDDR (Hydrogenation - …The invention relates to a hydrogen decrepitation process for sintered Nd-Fe-B permanent magnets and belongs to the technical field of magnetic materials. The hydrogen decrepitation process includes melting metal materials, quickly solidifying the metal materials into cast pieces, activating the cast pieces under a certain condition, namely …Dec 25, 2017 · Recycling of Nd-Fe-B magnets is one of the few solutions to alleviate the supply risks of certain rare earth elements (REE) such as Nd and Dy. One of the most promising solutions with regards to extraction of end-of-life (EOL) magnets is to apply hydrogen decrepitation and to physically separate the Nd-Fe-B as a demagnetized hydrogenated powder. Sep 14, 2000 · This way of powdering known as hydrogen decrepitation (HD) is a well-established stage of manufacturing technologies of sintered [2], [3] and bonded [4] Nd–Fe–B magnets. The interstitial hydrogen in the ferromagnetic Nd 2 Fe 14 B phase reduces significantly its anisotropy field H A. That is why desorption of hydrogen is necessary in order ...
A Hydrogen Decrepitation Press-Less Process (HD-PLP) recycling method for recycling of anisotropic NdFeB magnets is demonstrated. The method combines hydrogen decrepitation (HD) disintegration of the initial magnet, powder sieving and the Press-Less Process (PLP), where hydride powder is sintered in a graphite mold.
The process of hydrogen decrepitation (HD), which is used in the primary production and recycling of Nd magnets, takes place at low temperatures, even at room temperature, so that the entire microstructure decomposes only in powder form and the grain size is reduced. Sprecher, et al. [8] compared the environmental impact of producing virgin NdFeB magnets to producing recycled NdFeB magnets from waste computer hard disk drives (HDDs) using hydrogen decrepitation. The results showed that recycling in general was more favorable to the environment, and this was especially true for manual …
Due to the high strength and very compact structure of sintered NdFeB magnets, hydrogen decrepitation is a necessary step to break down the magnet mass. On the other hand, the resin-bonded NdFeB magnets have very low strength and can be easily crushed by heating and removing the resin and epoxy used in their fabrication. 39. 3.Investigating the properties of recycled NdFeB magnets. We report investigations on the processing by Spark Plasma Sintering (SPS) of RE Fe B (RE Abstract 2 14 = Nd, Pr. . . ) powders obtained by hydrogen decrepitation of decommissioned magnets and the magnetic properties of the consolidated magnets.Jul 14, 2000 · The decrepitation process and related changes in the sample temperature are analysed to explain the experimentally observed weight gain curve of a Nd–Fe–B sample due to hydrogen uptake. It is shown that the expansion of the specific surface resulting from decrepitation of the sample is the most important parameter controlling the hydrogen ... For the second type, three popular techniques, hydrogen decrepitation (HD), HDDR, and MS are applied to produce magnetic powders with the waste magnets. Note that the resultant powders prepared from the three techniques are single crystal powders, textured polycrystalline powders, and random aligned polycrystalline powders, respectively. ...The scrap sintered Nd–Fe–B magnets were recycled as the raw materials for bonded magnets using the hydrogen decrepitation (HD) process. The HD powders have the lowest oxygen and hydrogen content by hydrogenation at 150 °C with 1 bar H2 pressure and dehydrogenation at 600 °C. The powders with the largest particle size (>380 μm) …
Investigating the properties of recycled NdFeB magnets. We report investigations on the processing by Spark Plasma Sintering (SPS) of RE Fe B (RE Abstract 2 14 = Nd, Pr. . . ) powders obtained by hydrogen decrepitation of decommissioned magnets and the magnetic properties of the consolidated magnets.
There are many major production steps –plus numerous sub steps- in the manufacture of high-quality, high-tech Neodymium magnets. Each step is highly important, and each step is an essential part of a highly refined …
May 5, 2023 · The first is the hydrogen decrepitation (HD) process, which is already used in the primary production of NdFeB magnets to convert the alloy into powder form before further comminution. 46 The second process, named HDDR, which consists of two different steps, namely hydrogenation–disproportionation (HD) and desorption–recombination (DR), was ... An effective and complete processing route for the recycling of sintered Nd-Fe-B scrap magnets was proposed. Sintered Nd-Fe-B magnets were subjected to the Hydrogen Decrepitation (HD) process at various temperatures in the range of 50–300 °C, at two different pressures, 50 kPa and 200 kPa, followed by vacuum dehydrogenation in …magnets from electrical and electronic equipment. These materials are then processed using hydrogen decrepitation to transform the NdFeB magnets into a hydrogenated powder. This powder can then be extracted mechanically from the obsolete devices, and can then be processed further to produce either sintered or bonded rare earth magnets. The ultrafine magnet waste (particle size < 1 µm) contained around 50% rare earths mainly in the form of hydroxides as they are generated from the hydrogen decrepitation. The major phases in ultrafine NdFeB waste were Nd(OH) 3, Fe 2 O 3 and Fe phases. When ultrafine magnet waste was leached with hydrofluoric acid, all the iron …Dec 25, 2017 · Recycling of Nd-Fe-B magnets is one of the few solutions to alleviate the supply risks of certain rare earth elements (REE) such as Nd and Dy. One of the most promising solutions with regards to extraction of end-of-life (EOL) magnets is to apply hydrogen decrepitation and to physically separate the Nd-Fe-B as a demagnetized hydrogenated powder.
In this paper we describe and discuss the use of hydrogen in the processing ofNdFeB-type magnets. The roles of hydrogen in the hydrogen decrepitation (HD) and …The intrinsic magnetic coercivity (H ci) of Nd‐Fe‐B‐based permanent magnet material is profoundly affected by hydrogen absorbed during the hydrogen decrepitation (HD) process for producing anisotropic powders from bulk anisotropic hot‐deformed MAGNEQUENCH (MQ) magnets.Hydrogen (H) content and x‐ray diffraction …The gravimetric measurements also confirmed that Dy additions increase both the initiation and absorption time for hydrogen decrepitation. Hence, a higher hydrogen pressure will be required to speed up the process. AB - Scrap containing NdFeB is a valuable resource for the production of NdFeB magnets as the demand for these materials grows.@article{osti_37277, title = {Hydrogen decrepitation of sintered NdFeB magnets}, author = {Stiller, C and Roth, S and Binner, A}, abstractNote = {The kinetics of the hydrogen absorption and desorption behavior of a NdFeB sintered magnet is studied. Hydrogenation at temperatures above 200 C is used to crumble the Nd-enriched phase. …Oct 25, 2015 · End-of-life NdFeB magnets are important secondary RE sources. Several recycling methods for NdFeB magnets have been developed, such as direct reuse,4 hydrogen decrepitation (HD) and regeneration of new NdFeB,5–7 pyrometallurgical methods,8,9 hydrometallurgical methods,10–13 gas-phase extraction. The processing and characterisation of recycled NdFeB based magnets. S. Adrwish. Materials Science. 2013. The scrap magnets were turned into a powder using the HD process. The powder was milled for specific times and sintered for 1-3hrs at 1090 °C. The magnet samples were measured using a permeameter to…. Expand. PDF.
Feb 5, 2009 · Abstract. Some fully dense, sintered NdFeB-type magnets (employed in VCM disc drives) have been subjected to a recycling process using the hydrogen decrepitation (HD) process. After a brief milling treatment, the powder was aligned, pressed and re-sintered and this procedure was repeated four times with a progressive fall in the density and in ...
magnets from electrical and electronic equipment. These materials are then processed using hydrogen decrepitation to transform the NdFeB magnets into a hydrogenated powder. This powder can then be extracted mechanically from the obsolete devices, and can then be processed further to produce either sintered or bonded rare earth magnets. The process of hydrogen decrepitation (HD), which is used in the primary production and recycling of Nd magnets, takes place at low temperatures, even at room temperature, so that the entire microstructure decomposes only in powder form and the grain size is reduced. Electrolytic Hydrogen Decrepitation of NdFeB Magnets Under Ambient Conditions. V. Kaplan, Y. Feldman, …, I. Lubomirsky. Journal of Sustainable Metallurgy • Volume 8, Issue 3 • 1 September 2022. 1 citation; Scopus record. Article. 2D Pb-Halide Perovskites Can Self-Heal Photodamage Better than 3D Ones.Jul 14, 2000 · The decrepitation process and related changes in the sample temperature are analysed to explain the experimentally observed weight gain curve of a Nd–Fe–B sample due to hydrogen uptake. It is shown that the expansion of the specific surface resulting from decrepitation of the sample is the most important parameter controlling the hydrogen ... Abstract: Hydrogen decrepitation (HD) is an effective and environmentally friendly technique for recycling of neodymium-iron-boron (NdFeB) magnets. During the …The hydrogen-absorbing NdFeB powder absorbs heat in the plasma and rapidly decomposes and dehydrogenates. At the same time, in the dehydrogenation process, the particles are cracked and broken to form fine NdFeB powder due to rapid heat absorption and release of a large amount of hydrogen, and the NdFeB powder is at a high …The fabrication of Nd-Fe-B sintered magnets is composed of quite a few processes mainly including strip casting, hydrogen decrepitation, jet-milling, magnetic alignment and pressing, sintering and subsequent heat treatment, machining, and surface coating. ... Possible methods of recycling NdFeB-type sintered magnets using the …
NdFeB-based alloys and magnets also react readily with hydrogen, and this has been exploited by the hydrogen decrepitation (HD) process [4]. During HD the material is exposed to hydrogen (at room temperature) and initially the Nd-rich phase absorbs hydrogen (represented approximately by Eq.
Sagawa obtained ultrafine NdFeB grain by innovative HD (hydrogen-decrepitation) + HDDR (hydrogenation-disproportionation-desorption-recombination) + helium jet milling process. It should be noted that the helium gas is more suitable than nitrogen gas to fabricate ultrafine powder due to its lighter mass fraction, and will also …
room temperature in a custom-made gauge glass reactor, and the hydrogen decrepitation process was video-monitored in situ with a single frame camera at 0.1 frames per second (fps).Sagawa obtained ultrafine NdFeB grain by innovative HD (hydrogen-decrepitation) + HDDR (hydrogenation-disproportionation-desorption-recombination) + helium jet milling process. It should be noted that the helium gas is more suitable than nitrogen gas to fabricate ultrafine powder due to its lighter mass fraction, and will also …The process of hydrogen decrepitation (HD), which is used in the primary production and recycling of Nd magnets, takes place at low temperatures, even at room temperature, so that the entire microstructure decomposes only in powder form and the grain size is reduced. The obtained strips were pulverized and further milled into ∼5 μm powder using hydrogen decrepitation and jet milling, respectively. These powders were pressed in a magnetic field of 1.8 T under a pressure of 8.0 MPa. Afterward, the green compacts were sintered at 1070°C for 3 h in vacuum, cooled by Ar quenching. ... NdFeB sintered …The Hydrogen Decrepitation and the Hydrogen Disproportionation Desorption Recombination processes for the preparation and the recycling of the two industrially produced phases of SmCo alloys, SmCo5 and Sm2Co17, are reviewed. The effects of the chemical composition, the microstructure, the exposure time, the hydrogen …Aug 4, 2022 · One of the most promising solutions with regards to extraction of end-of-life (EOL) magnets is to apply hydrogen decrepitation and to physically separate the Nd-Fe-B as a demagnetized... The Nd 2 Fe 14 B phase is the main component of sintered NdFeB magnets. The ternary NdFeB phase diagram (Fig. 5.1(a)) shows that there are five phases in addition to the Nd 2 Fe 14 B (T1) phase: Fe, Nd 2 Fe 17, Nd 5 Fe 17, Nd 1.1 Fe 4 B 4 (T2), and Nd.Sintered NdFeB magnets are produced by the liquid phase sintering process and the …The method combines hydrogen decrepitation (HD) disintegration of the initial magnet, powder sieving and the Press-Less Process (PLP), where hydride powder is sintered in a …
Mar 14, 2016 · Hydrogen decrepitation (HD)/hydrogenation disproportionation desorption recombination (HDDR) is a process used in manufacturing REPM and carried out as pretreatment before green body sintering. During hydrogenation, the Nd-rich grain boundary phase in NdFeB magnets initially absorbs hydrogen forming Nd hydride: [ 49 ]. Introduction. In the fields of sintered magnets, the hydrogen decrepitation (HD) technique has been widely used. The as-melted NdFeB bulk material becomes brittle after HD and decrepitates into powders, as a result of the large volume expansion of the lattice of both the Nd 2 Fe 14 B matrix and the intergranular Nd-rich phase [1]. Hydrogen …Instagram:https://instagram. blogh2577 014the real deal about hypoallergenic fabricsbandb theatres ozark nixa 12georgetown men room temperature in a custom-made gauge glass reactor, and the hydrogen decrepitation process was video-monitored in situ with a single frame camera at 0.1 frames per second (fps). is there a long john silverpercent27s near meyhrj NdFeB ingot exposed to hydrogen atmosphere due to the changes of hydride lattice parameters cracks. The process called HDDR (Hydrogenation - …In this paper it is demonstrated that hydrogen could play a vital role in this process. Fully dense, sintered NdFeB-type magnets have been subjected to the … blogh2577 014 Jan 1, 2006 · Several recycling methods for NdFeB magnets have been developed, such as direct reuse,4 hydrogen decrepitation (HD) and regeneration of new NdFeB,5–7 pyrometallurgical methods,8,9 hydrometallurgical methods,10–13 gas-phase extraction. Direct reuse is only suitable for large magnets, such as those used for wind turbines, electric motors, and ... Hydrogen decrepitation (HD) is an effective and environmentally friendly technique for recycling of neodymium-iron-boron (NdFeB) magnets. During the HD process, the …Jul 1, 2019 · Recycling of scrap sintered Nd–Fe–B magnets as anisotropic bonded magnets via hydrogen decrepitation process. The scrap sintered Nd–Fe–B magnets were recycled as the raw materials for bonded magnets using the hydrogen decrepitation (HD) process. The HD powders have the lowest oxygen and hydrogen content by….